Sustainable fashion may dominate headlines today, but when Sachin Malik first joined the textile industry 17 years ago, it was a far less urgent priority. Over nearly two decades, he’s watched the conversation shift, from small-scale initiatives to a sweeping transformation of the entire value chain.
“When I started in this industry, sustainable fashion was more of a niche idea,” he reflects. “Today, it’s a necessity.”
Now serving as Commercial Head at Asia Pacific Rayon (APR), Sachin is helping to drive that change at scale. For him, the appeal of the industry lies not only in the evolution of materials, but in the constant potential to explore new markets, products, and innovations.
“We remain extremely positive about the growth in this space, compared to some of the other players out there,” he says. “We believe in its potential, and we can continue to grow our capacities and markets. When we develop new products, reach out to new customers, and explore new applications and innovations – that’s what keeps me engaged in this industry.”
His current focus is lyocell fibre, an innovation he believes is not just an alternative, but an essential part of the future of fashion.
How Lyocell Fibre is the Future of Fashion
Lyocell fibre has been around for decades, often praised for its environmental benefits, but has only recently gained real traction in the mainstream. A cellulosic fibre made from renewable wood sources, lyocell is considered one of the most sustainable fibres available today.
“We’re at a tipping point,” he says. “The growth we saw in those first 30 years? We are about to match that in just one year.”
What sets lyocell fibre apart is its unique combination of sustainability and performance. Produced through a closed-loop process that recycles over 99% of solvents, the fibre requires far less land and water than cotton. It is biodegradable, breaks down within weeks, and offers a low-impact solution without compromising on quality.
As cotton production comes under increasing pressure from land and water scarcity, lyocell fibre offers a viable alternative. “We see lyocell fibre increasingly meeting the demand that cotton cannot, especially as land competition grows,” Sachin explains. “With its combination of sustainability and performance, lyocell fibre is positioned as a serious alternative. Our focus is on making it more accessible, available at scale, and cost-effective.”
He acknowledges that fast fashion isn’t disappearing overnight, but the materials powering it can change. Making lyocell fibre competitive on price is a crucial step toward making sustainable fashion a global norm.
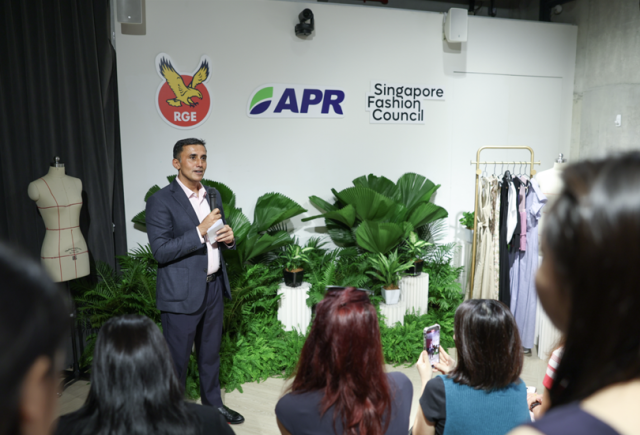
Sachin Malik, Commercial Head of Asia Pacific Rayaon (APR) discusses the future of lyocell fibre.
Scaling Up: The 1 Million Tonne Vision
Backed by RGE’s global resources and long-term commitment to sustainability, APR is scaling up its lyocell fibre capabilities to meet surging demand.
The lyocell sold by APR to customers in Asia and around the world is manufactured by sister company Sateri. Both are members of the RGE group of companies
But that’s only the beginning.
“We have ambitious plans – to grow lyocell fibre production to 1 million tonnes” Sachin says.
Lyocell fibre production is growing at an annual rate of 30–40%, and APR is ready to respond to rising demand. With increasing price competitiveness versus cotton and viscose, Sachin believes the fibre will continue to gain traction across different applications.
“In collaboration with our colleagues in Sateri, we are confident that we will reach 1 million tonnes in the next three to five years,” he adds. “That helps us significantly reduce reliance on synthetic fibres, lower water and land usage compared to cotton, and accelerate the shift towards biodegradable, circular materials in the fashion industry.”
Partnering for a Sustainable Industry
Still, Sachin points out that producing more lyocell fibre isn’t enough. True impact comes from enabling its widespread use among industry players.
“It’s not just about making lyocell fibre,” he says. “We’re working across the entire value chain to make it easier to adopt.”
APR works closely with brands, textile manufacturers, and dyeing experts to solve practical processing challenges, ensuring that lyocell fibre can integrate seamlessly into current production systems. Education plays a big role here, with Sachin’s team helping partners understand how best to handle, dye, and finish lyocell fibre fabrics.
The company’s investment in research is also a core part of the story. RGE, of which APR is a member company, has partnered with Nanyang Technological University to launch the RGE-NTU Sustainable Textile Research Centre (SusTex), a S$6 million initiative focused on advanced recycling solutions. One key area of research is the separation of mixed and blended textiles – materials that dominate post-consumer waste streams in densely populated cities. In these urban recycling environments, where garments are rarely sorted by fibre type and often made of complex blends, scalable solutions for textile-to-textile recycling are urgently needed. SusTex aims to close this gap by developing technologies that support fibre recovery at scale, helping move the industry closer to true circularity.
“We’re not just talking about sustainability,” Sachin says. “We’re building real, scalable solutions.”
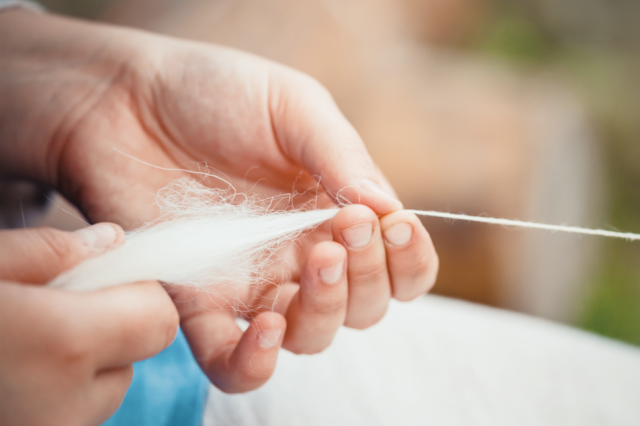
Lyocell fibre is derived from renewable materials and fully biodegradable.
Breaking Industry Misconceptions
Despite its clear environmental and performance benefits, lyocell fibre continues to face a common misconception: that all man-made fibres are harmful to the environment.
“People hear ‘man-made fibre’ and assume it’s synthetic,” Sachin explains. “That’s one of our biggest challenges.”
Unlike polyester, lyocell is made from renewable wood sources and contains no fossil-derived materials. It is fully biodegradable and leaves no long-term waste, but it’s often mischaracterised because it’s produced through an engineered process. Yet as Sachin notes, sustainability is not about whether a fibre is natural or man-made, but about how it’s sourced, produced, and disposed of.
“Unlike synthetic fibres that can sit in landfills for centuries, lyocell fibre is derived from renewable materials and breaks down naturally,” he says. “It’s time to change the perception of what sustainable textiles can be.”
A Vision for the Future of Fashion
Looking ahead, Sachin is optimistic not just about scale, but about impact. Beyond market growth, he believes that lyocell fibre is a key enabler of a circular fashion economy.
“By 2030, the lyocell fibre market is expected to grow manifold,” he says. “The market is expanding quickly, but for me, the real impact is not just in production numbers. It’s about how lyocell fibre is moving beyond niche use cases into mainstream, everyday textiles, making sustainability more accessible across the industry.”
More than ever, lyocell fibre is appearing in everyday garments, from high-street fashion to home textiles and performance wear. As APR works with its partners to bring down costs and improve access, it’s becoming an increasingly viable option in emerging markets as well, and it continues to drive innovation through active collaboration with partners to explore solutions for textile recycling and sustainability challenges.
“What excites me the most is seeing people in developing markets finally have access to sustainable fabrics at an affordable price,” Sachin shares. “We’re seeing this shift firsthand. Lyocell fibre is no longer just for premium brands. As we scale up production and continue working with brands and textile processors, sustainable fibres are becoming more available and widely adopted. This is a big step forward in ensuring sustainability isn’t just a luxury, but an industry norm.”
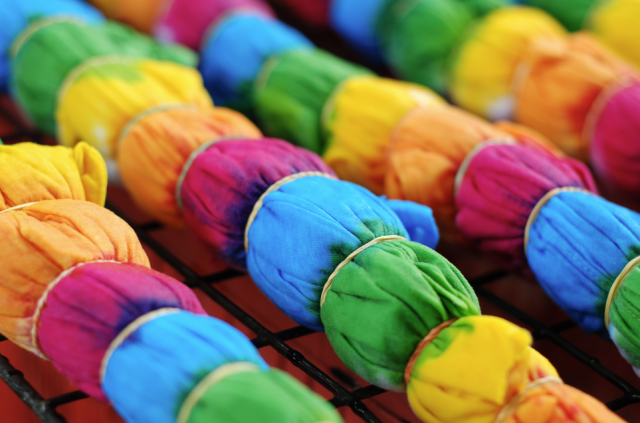
From high fashion, performance wear, to home textiles, lyocell fibre has versatile uses.
The Drive to Make Sustainability a Reality
From Sachin’s perspective, the pathway to transforming the textile industry is already taking shape. With growing alignment across the value chain, from producers to brands to consumers, the moment to act is now.
“Lyocell fibre is growing at an unprecedented rate, and we remain committed to expanding its adoption across the textile industry,” he says. “We have the technology, we have the demand, and now it’s about execution. The future of textiles is sustainable, and lyocell fibre is leading the way.”